DegreeSign product design and manufacturing process is vertically integrated with a special focus on products usability, manufacturability, and durability.
Start with an idea or a challenge and get an end-solution tailored to your target market. Design with a lean approach that fits your budget, optimised for your business goals and target users.

Product Research
Find out if your challenge is practically solvable.
DegreeSign research process is very comprehensive. Get advice on your specific idea or challenge. We listen to your challenge and recommend suitable solutions. Planning a new product development takes into account specifics that vary from one challenge to another. Fruitful projects start with a development plan. DegreeSign planning helps you cover all initial blind spots, saving you time and money.
Planning call
Identify project objectives, expectations, and root causes of various challenges. Assess the technical feasibility of the project and set the next steps. The project planning call can also identifies:
✓ Design direction, e.g. plastic vs metal
✓ Technology direction, e.g. old vs new
✓ Fabrication direction, e.g. forming vs machining
✓ First iteration/patch cost estimations
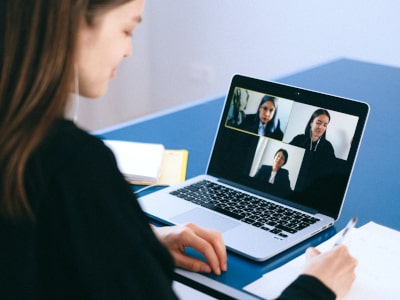
Product research
A line chart representing how market trends for a given consumer product can be measured. Conduct market and technology research to assess your new product idea against readily available ideas and products on the market. The research investigates active competition and ideas that could develop into competing products in the not-distant future.
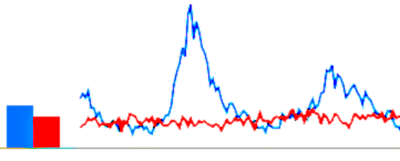
Feasibility study
The feasibility study delivers an understanding of the industry landscape. It is also assisted by a preliminary review of past and current valid intellectual property (IP) to gauge the feasibility of designing proposed solutions. Projects can include travel and on-site visits to evaluate challenges, where communication with end-users and stakeholders can help set and evaluate design goals. A survey of prices offered for competitor products can also be done to estimate possible savings an innovation could bring.
Development plan
Get a written plan tailored to your project. It starts with a concluded brief, and goes through the execution methodology and recommended production options. The product development plan includes a breakdown of the product development stages with their estimated cost along an expected timeline. The development plan could also be visualised as a mind map diagram.
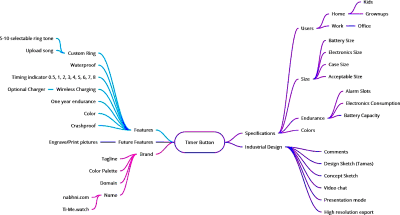
Product Design
Design a single part solution or include hundreds of parts.
Product engineering design for manufacturing turns initial concepts into practical designs, using a staged design process. The process develops concepts into detailed designs accounting for all functionalities. Designs are validated using various product prototypes and tests.
Concept sketches
Visualise winning ideas and features using 2D hand-sketches.
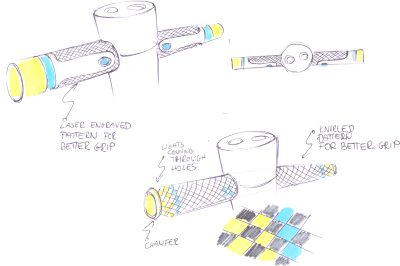
A group of sketches for the handles portion of a consumer mobility product. The conceptual design is done in cycles until a healthy number of iterations is generated, where concepts define the overall look and feel of the product. Feasible ideas are shaped to achieve set goals with features selected to enhance the efficiency and manufacturability of the product.
Concept design
Capture the initial vision in a realistic 3D representation
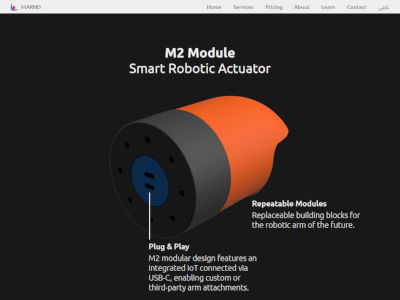
Concept 3D renders are created based on the initial vision of the product. These concepts are crucial these days to communicate ideas. Stakeholders expect them for any new physical product. These concepts are excellent for landing pages to verify demand and gather support for new ideas. If no funds are available for the project, a landing page (one-page website) can kick start funding efforts from individual angel investors, industry veterans, or as a place to collect emails for a crowdfunding campaign offering pre-sales of product, for example on Kickstarter.com
CAD design
Turn the vision into a product in native 3D environment
The CAD engineering design process starts with a preliminary design that bridges the gap between conceptual and detailed design. Create all supporting features then reviewed through mockups and draft renders to be approved for detailed engineering design.
The detailed product engineering design defines all intricate details, e.g. sub-components, dimensions, and tolerances. It facilitates more accurate estimations of product specifications and cost, and more importantly, allows for successive product prototyping and test.
Electronics design
Technological elements, such as electronic components, are designed and integrated into the system of the new product. The integration process leads to a product prototype development that is production-ready at an early stage of the design process. An example is printed circuit boards (PCBs) designed directly using final surface-mounted components (SMD), instead of going through breadboard iterations using larger components.
Product prototype
Physical product prototyping follows, using 3D printing to create functional models to test mechanical parts. Each printing process is followed by tests to gauge parts characteristics, such as relative size, functionality and strength.
Tests are initially carried out by simulating real-world scenarios digitally. These identify how parts of the new product could change or break under expected loads. They estimate design limitations and help identify possible improvements.
Under-stressed areas identified during tests are a good example. Those areas often signal excess material that could be removed without impacting functionality, thus saving weight and cost.
Product prototype parts are initially produced on filament-based 3D printers (FDM), while smaller and more accurate parts are produced using powder-based SLS printers (selective laser sintering) or CNC machines (computer numerical control) to achieve lower tolerances (better accuracy).
Product Manufacturing
Final engineering design optimisation of the new product for manufacturing. Industry-level technical drawings and files, ready to share with global manufacturers. Produce pre-production samples and conduct deployment tests. Set up a global efficient supply chain. Manage mass production with ease up to quality control and products dispatch.
Design optimisation
Throughout the product prototyping cycle, test results are reviewed to highlight challenges and areas for improvement within the new product.
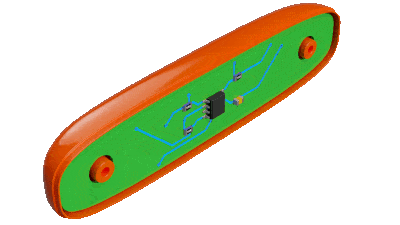
This process is cyclic and usually require the repetition of product prototyping and tests. The design is to be frozen once the improvement between cycles goes below a relatively low percentage. The engineering design of the new product is then improved by correcting any deficiencies and optimising parts and assemblies performance to provide maximum efficiency.
Technical documentation
Technical drawings and files communicate important “controlled” features using a universally understood format, e.g. specifications, dimensions, and tolerances. They help suppliers understand product requirements and facilitate communication regardless of experience level, country or even language.
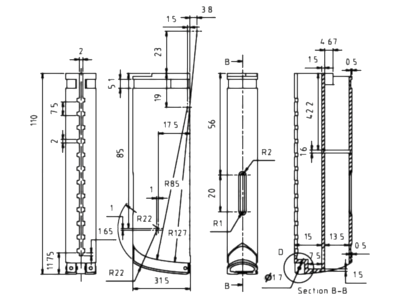
These documents are usually produced in PDF format, easily printable by any suppliers and do not require any specific technical program to review. Documentation is a crucial element in the production process. In some cases, these documents could be also be used in a legal capacity, as they can verify production quality limits.
Pre-production samples
Pre-production samples of the new product are made to verify the actual functionality, specifications, and product aesthetics. Required improvements can be fed back into an engineering design review and optimisation loop for additional samples, before investing in mass production moulds and jigs.
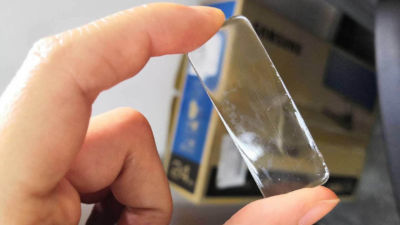
Supply chain setup
Product parts BOM (bill of materials) is divided according to shared manufacturing processes into several sets. Potential manufacturers of each set are sent RFQs (request for quotation) for order placement. For larger projects, on-site visits can be conducted to evaluate relevant preparations.
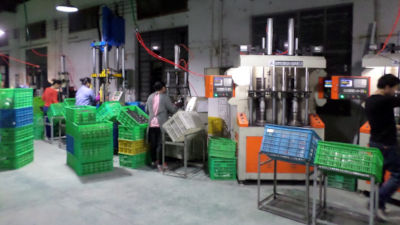
Production management
The supply chain is continuously monitored against a set of milestones and deadlines to resolve challenges that may arise. Sub-processes are reviewed for quality assurance to avoid challenges in later production stages, e.g. on the assembly line. The assembly process is reviewed for setup improvements and quality maintenance, while on-site checks ensure the production progresses according to requirements.
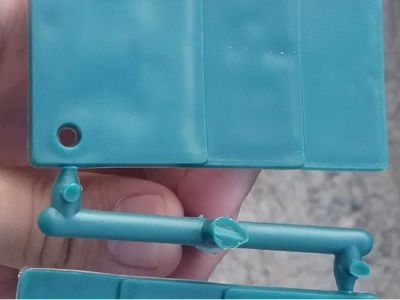
Quality control
Final parts and assemblies are reviewed to verify dimensional conformity, performance, and other specifications.
For the initial production patch, non-confirming units can be a significant percentage, but supplementary production helps achieve the required order size. Product patches that pass quality control are packaged and shipped according to requirements.
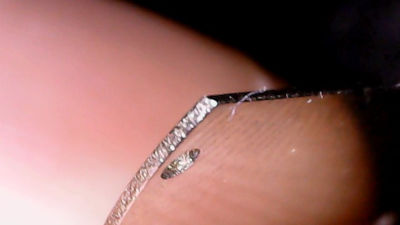
Marketing materials
Including marketing materials, manuals and other items are equally important to be accurate and pleasant to see, if not read. Gimmicky features such as magnets in off-shelf ready-made packaging reflect poorly on the product perceived quality. Represent new products in the best light using digital marketing material made for the web, in addition to physical materials ex. product packaging and brochures.
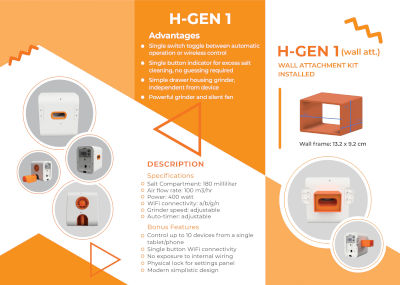
Packaging represents the first user experience with the product and favouring the shipping durability over the packaging promotional appearance can make sense for some packages. Digital marketing materials are also crucial for selling online, as eCommerce continues to grow its share from conventional retail businesses. These digital photorealistic renders are more versatile and appealing the photos, especially to highlight small features of products that might otherwise show dust in photos.